Flexo Printing Machine
In recent years, Flexo Printing Machine has made great progress in my country with its unique advantages in the field of packaging printing. According to statistics, more than 150 Flexo Printing Machine production lines have been introduced in China, and more than 7 domestic printing machine manufacturers have begun to produce narrow-width unit Flexo Printing Machines. The Flexo Printing Machine method has been accepted by more and more people in the domestic packaging printing industry.
Flexo Printing Machine was originally called aniline printing. It originated in the United States in the early 1920s. It did not develop because the aniline dye ink it used was toxic. After the mid-1970s, due to the progress of the materials industry, especially the advent of polymer resin plates and metal ceramic anilox rollers, the development of Flexo Printing Machine has made a qualitative leap and has become the fastest growing printing method in the world. Especially in the United States, it has been fully developed. Both the manufacturing technology of printing machines and the application technology of Flexo Printing Machine represent the highest level of Flexo Printing Machine. Most of the commodity packaging seen in the domestic market of the United States is almost Flexo Printing Machine products. According to statistics, in the United States, the market share of Flexo Printing Machine in the field of flexible packaging printing accounts for 70%, in the field of label printing accounts for 85%, in the field of corrugated box printing accounts for 98%, and in the field of paper box printing accounts for 25%. In Europe, the market share of Flexo Printing Machine in the above packaging fields also accounts for 60%, 35%, 85% and 3% respectively. In the United States, even 20% of newspapers are printed with Flexo Printing Machine. This is enough to prove the vitality of Flexo Printing Machine.
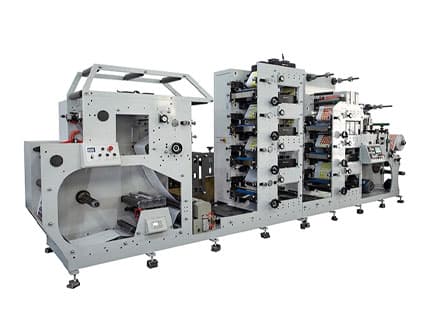
The difference between Flexo Printing Machine and other printing methods lies in its unique characteristics. First, it uses soft polymer resin plates, which reduces the plate-making cost and shortens the plate-making cycle compared to gravure printing. Due to the improvement of plate manufacturing level and plate-making technology, the screen plate can now reach 175 lines/inch, which is enough to meet the needs of general packaging printing. Second, it uses anilox rollers, which are both ink transfer rollers and ink metering rollers, achieving the same short ink path as gravure printing, and can accurately supply ink according to process requirements. Currently, the metal ceramic anilox rollers engraved by laser can reach 1600 lines/inch, which provides a favorable means for accurately controlling ink color and ink layer thickness. Third, zero-pressure printing reduces vibration and wear on the machine and the plate, and also expands the range of printing media, especially for the printing of flexible materials. Fourth, the narrow-width Flexo Printing Machine also expands the function of the printing machine. In addition to printing, it can complete a large number of post-printing processes, making the Flexo Printing Machine a production line integrating printing and post-printing processing.
The strengths of Flexo Printing Machine are most prominent in the field of packaging printing, mainly reflected in:
1. Thick ink layer and consistent ink color. Although the ink layer of Flexo Printing Machine is thinner than that of gravure printing, it is definitely thicker than that of offset printing, which is very beneficial for printing large-area color blocks commonly seen in packaging products; because of the use of anilox rollers to transfer ink, generally speaking, if the paper and ink conditions remain unchanged, the ink color of products from the same batch or different batches can remain consistent, which is the most basic requirement for packaging printing and is not easy to achieve with offset printing.
2. Widely use non-toxic water-based ink for printing. Flexographic ink is the only non-toxic ink approved by the US Food and Drug Association among all printing inks currently available. Therefore, Flexo Printing Machine is also called green printing and is widely used in instrument and drug packaging, which is beyond the reach of other printing methods.
3. Wide range of suitable printing media. Flexo Printing Machines can not only print various types of paper, but also aluminum foil, plastic film, self-adhesive paper, self-adhesive film, cellophane, metal foil and textiles. The types of suitable printing media are more than those of gravure printing. The offset printing method cannot or is not easy to print on other media except paper.
4. The product has a wide range of applications. Almost all paper and plastic packaging products can be printed by Flexo Printing Machine, and the printing effect on plastic film is comparable to gravure printing. In addition to packaging products, newspapers, books, magazines and other products can also be printed.
5. The equipment has strong comprehensive processing capabilities. Almost all narrow-width unit-type Flexo Printing Machines can be processed after printing on the same equipment, such as reverse printing, glazing, laminating, die-cutting, cross-cutting, slitting, punching, dragon-punching, fan-folding, automatic waste discharge, etc., and even numbering, hot stamping or screen printing units can be added to the printing unit. Therefore, it is not unreasonable for some people to call the Flexo Printing Machine a printing and processing production line.
6. Low production cost and high economic benefit. Compared with gravure printing, Flexo Printing Machine has a short plate-making cycle and 30% lower plate-making costs; ink consumption is 30% less than gravure printing; electricity consumption is saved by 40%; printing speed is fast, and the printing speed of general unit-type narrow-width Flexo Printing Machines can reach 150 meters per minute, and the printing speed of satellite-type wide-width Flexo Printing Machines can reach more than 350 meters per minute; the scrap rate is lower than that of gravure and offset printing; it occupies less production space; it has strong comprehensive processing capabilities, one-time molding, saving labor in the subsequent process; and avoiding the waste of turnover between processes.
7. Small production investment. Due to its relatively simple structure, the equipment investment of Flexo Printing Machines is lower than that of offset or gravure printing machines of the same scale, which can generally save 30% to 40%. In addition, as far as narrow-width Flexo Printing Machines are concerned, since they have almost most of the post-printing processing functions, users who purchase Flexo Printing Machines do not need to purchase post-printing processing equipment such as die-cutting and glazing, thus saving this part of investment. At the same time, it also saves the space and labor occupied by this part of equipment. If Flexo Printing Machine is compared with gravure printing, all products that can be printed by gravure printing can be printed by Flexo Printing Machine, and can reach or approach the quality level of gravure printing, while flexible materials that can be printed by Flexo Printing Machines cannot be replaced by gravure printing; in addition, in terms of equipment investment and use costs, Flexo Printing Machine is much lower than gravure printing. Undoubtedly, using Flexo Printing Machine for packaging printing production is a wise choice with low investment and high output.
Although Flexo Printing Machine can achieve higher precision, its high-precision screen image quality cannot be compared with offset printing due to the reasons of relief printing and anilox roller ink transfer. In the field of high-end albums and book printing, the offset printing method is undoubtedly superior to Flexo Printing Machine, but in the field of packaging printing, Flexo Printing Machine has incomparable advantages over offset printing. First of all, consistent ink color is the most basic requirement for packaging printing. Since offset printing has the problems of water-ink balance and ink emulsification, consistent ink color has become a big problem for offset printing, and this is the strength of Flexo Printing Machine. Secondly, packaging design has a large number of color blocks and icons. In addition to the ghosting problem, offset printing also has an insufficiently thick ink layer. When encountering large areas of spot color blocks, it has to be printed twice or even three times, while the ink layer thickness of Flexo Printing Machine is far greater than that of offset printing. Furthermore, packaging products rarely have a positive opening number. If a double-opening or four-opening platform offset printing machine is used, the first print will have more or less waste edges. However, if a Flexo Printing Machine is used for rotary printing, the knife edge and seam can be accurately reserved to the millimeter, thus saving a lot of paper. In addition, when printing packaging products by offset printing, post-printing processing such as glazing and die-cutting is still required after printing, which requires both equipment and manpower. However, a Flexo Printing Machine that integrates printing and post-printing processing can complete all processes at one time, which not only saves equipment investment, but also reduces the consumption caused by turnover between processes, shortens the production cycle, and its efficiency is incomparable to offset printing. In addition, the printing life of Flexo Printing Machine plates can usually reach 1 million to 3 million times, while offset printing plates can only print hundreds of thousands of times after processing. Therefore, although the cost of Flexo Printing Machine is high, the printing life of the plate material is also high. For long-run jobs, the average platemaking cost of a single product is flat. Finally, in addition to paper, other printing media are not suitable for offset printing. Even paper has a certain thickness range limit. On Flexo Printing Machines, plastic films and metal foils can be printed, and the thickness range of paper printing is also large.
Currently, Flexo Printing Machine has been widely used in various packaging and printing products. In the United States, self-adhesive labels have become the main product of Flexo Printing Machines. Flexo Printing Machines can complete almost all label printing processes, such as die-cutting, embossing, waste discharge, glazing, laminating, peeling off the film and then flipping and printing and laminating. In addition, the printing of packaging cartons is another major source of business for Flexo Printing Machines. In addition to labels, products suitable for narrow-format Flexo Printing Machines include paper packaging for various commodities, folding cartons, cultural supplies, paper bags, paper cups, paper tableware, wallpaper, etc. Products suitable for wide-format Flexo Printing Machines include various plastic films, vacuum aluminized films, and pure aluminum foil packaging products.
In my country, Flexo Printing Machine started late, and it was not until the mid-1980s that simple stacked Flexo Printing Machines were introduced. In recent years, with the improvement of foreign Flexo Printing Machine technology, Chinese industry insiders have also had a new understanding of Flexo Printing Machine processes and technologies, and have begun to introduce various high-level Flexo Printing Machines. The introduction of any new technology will encounter more or less difficulties and problems, and Flexo Printing Machine is no exception. The first is the procurement of various supporting materials. There are many supporting materials required for Flexo Printing Machine, which needed to be imported a few years ago. In recent years, the rapid development of Flexo Printing Machine has driven the development of related material industries. Some related materials have begun to be produced in China and can replace imports. For example: ink manufacturers are already all over the country, and anilox rollers and die-cutting rollers have been produced in Shanghai. Although some still need to be imported, such as plates and tapes, purchasing them has become as simple as buying plate-making films. The second is the source of work. Compared with gravure printing, Flexo Printing Machine can be more flexible and diverse in the batch of work, but due to its high printing efficiency, it also needs a considerable source of work to start up normally. Taking cigarette packages as an example, a 16-inch Flexo Printing Machine must have at least 100,000 large boxes of business a year to be full. Thirdly, Flexo Printing Machine has its unique process characteristics. From pattern design to color selection, the strengths of Flexo Printing Machine should be highlighted and the weaknesses of Flexo Printing Machine should be avoided. However, there is still a lack of packaging designers who understand Flexo Printing Machine technology in China. Many products are directly transferred from offset printing to Flexo Printing Machine, which cannot make the best use of their strengths and avoid their weaknesses, reducing the satisfaction of end customers with flexographic products, thus affecting people's understanding and recognition of Flexo Printing Machine. In addition, the concept problem is also a problem that restricts the development of Flexo Printing Machine. In the past few years, there were two very extreme views. One is that Flexo Printing Machine is too good and will replace gravure printing and even offset printing in the future; the other is that Flexo Printing Machine is too bad and can only print very inferior products. These statements are biased. The correct positioning of Flexo Printing Machine should be: a low-input, high-output applicable technology in the field of packaging printing. Only by finding the correct positioning of Flexo Printing Machine can we find the market positioning.
Many brands of Flexo Printing Machines have been introduced in China, most of which are successful. However, some factories are more or less blind because they have little understanding of the characteristics of Flexo Printing Machine, and have taken detours, either choosing the wrong size or the wrong configuration. The only way to avoid taking detours is to learn more and fully understand the process characteristics of Flexo Printing Machine. Don't use the old experience of offset printing or gravure printing to explain the problems of Flexo Printing Machine. For example, the size problem, from the perspective of offset printing, the larger the number, the better, because more products can be produced under the same number of prints; but Flexo Printing Machine is not the case. Efficiency is achieved by machine speed. If the workpiece allows, the size is appropriate. Small size first means low cost of use. Small equipment size means small size from plate roller to die-cutting cylinder, and naturally saves plate material, tape, and plate making fees. Small size also means small cumulative error during operation, and quality control is easy. Of course, we cannot generalize. For printing plastic film, it is better to choose satellite wide-format machine because its tension change is easy to control. There is also the configuration issue. Don't blindly pursue redundant functions that are not used temporarily, because in fact the Flexo Printing Machine itself is a combination of multiple functions, which can be completed before leaving the factory or added during use.